How to Prepare for and Conduct a Health and Safety Risk Assessment
No one goes to work expecting an accident — but without the right precautions, it is a constant fear for many frontline workers. A single overlooked hazard can lead to injuries, costly downtime, or even legal trouble. That’s why regular health and safety risk assessments are so important.
They help businesses identify potential dangers, protect employees, and stay compliant with industry regulations. But beyond a simple legal necessity, it’s a responsibility — because ensuring your team’s safety should be more than just check-marking a legal box.
But how do you conduct a thorough risk assessment efficiently? Who should be involved? What steps can you take to turn safety planning into real, effective action?
Let’s answer those questions.
What is health and safety risk assessment?
A health and safety risk assessment systematically identifies workplace hazards, evaluates their risks, and proactively spots potential dangers before harm occurs. The goal is clear: determine what could hurt your employees and implement controls to prevent accidents, injuries, and work-related illnesses.
Typically, a risk assessment covers all physical, chemical, biological, and psychological dangers present in your workplace. A comprehensive assessment can also examine routine and non-routine tasks, including maintenance work, emergency procedures, and contractor activities.
While the fundamental principles remain consistent, the risk assessment process varies across industries due to their unique hazards:
- Manufacturing facilities focus heavily on machine guarding and chemical exposures.
- Construction sites prioritize fall protection, struck-by hazards, and temporary work environments.
- Offices concentrate on ergonomics and emergency evacuation.
The difference isn't just in what you assess, but how deeply you should investigate certain hazards — some industries require specialized technical assessments (like noise monitoring in manufacturing) that wouldn't be necessary in other surroundings.
Who conducts health and safety assessments — and how often
Health and safety assessments are typically handled by your in-house safety team — whether dedicated safety officers or trained managers who know the department's operations inside and out. For complex or dangerous hazards, like noise assessment, companies will often bring in outside consultants.
As for timing, you'll want to conduct them at least annually, but also whenever something significant changes — when you install new equipment, modify workflows, or after an incident.
Legal requirements vary across industries, with specific expectations for different sectors:
- Construction: Companies must assess risks like falls, equipment hazards, and structural failures, complying with OSHA standards (US) or Construction Design and Management (CDM) Regulations (UK).
- Healthcare: Facilities must evaluate biological hazards and infection risks, following CDC or WHO standards. Assessments include patient handling procedures, needlestick prevention, and ergonomic evaluations to prevent staff injuries during patient care.
- Chemical/manufacturing: Organizations need to assess chemical exposure risks, fire hazards, and equipment safety, following COSHH (UK) or OSHA's Process Safety Management standards. This often requires quantitative measurement of exposure levels against established safety thresholds.
- Transportation: Companies must evaluate vehicle operation risks, driver fatigue, and hazardous material handling and comply with standards like the Federal Motor Carrier Safety Administration (FMCSA) regulations. Regular vehicle inspection assessments are typically mandatory.
- Energy sector: Organizations handling oil, gas, or nuclear energy must conduct specialized risk assessments for explosion hazards, radiation exposure, and environmental impacts, following stringent international safety standards like those of the International Atomic Energy Agency or NRC.
There are other industries with specific regulations, but you get the gist.
How to prepare for an H&S risk assessment
Below are three essential things you should do before starting with the actual assessments.
Build a team
An effective health and safety assessment team needs both authority and practical knowledge. It might be a single competent person for a small operation or a dedicated team for bigger ones. The team, ideally led by a safety manager, will organize and conduct the assessment and present you with the report afterward.
While they do not have to be officially part of the team, try to include frontline workers in the process — they know the day-to-day realities of the job better than anyone.
Gather necessary information
Before your first walkthrough, collect all relevant documentation to build a solid foundation for the assessment. This typically includes previous risk assessments, relevant incident reports, equipment maintenance records, existing safety policies and procedures, chemical safety data sheets, and regulatory standards applicable to your industry.
This background work helps you highlight known problem areas you want to look extra hard into.
Establish goals and scope
Be crystal clear about what you're assessing and why. Is it an all-encompassing health and safety risk assessment?
If not, define specific objectives like "identify all ergonomic hazards in the packaging department." Then establish boundaries — are you assessing the entire facility or just one operation? All job functions or specific roles?
For example, a manufacturing plant might focus on "evaluating machine guarding and operator safety for the new production line in Building C, covering all shifts and operations." This clarity helps keep your assessments focused.
Steps for conducting H&S assessments
Now that you're properly prepared, it's time to take action. This step-by-step approach ensures that you identify all hazards, evaluate their associated risks, and develop effective control measures.
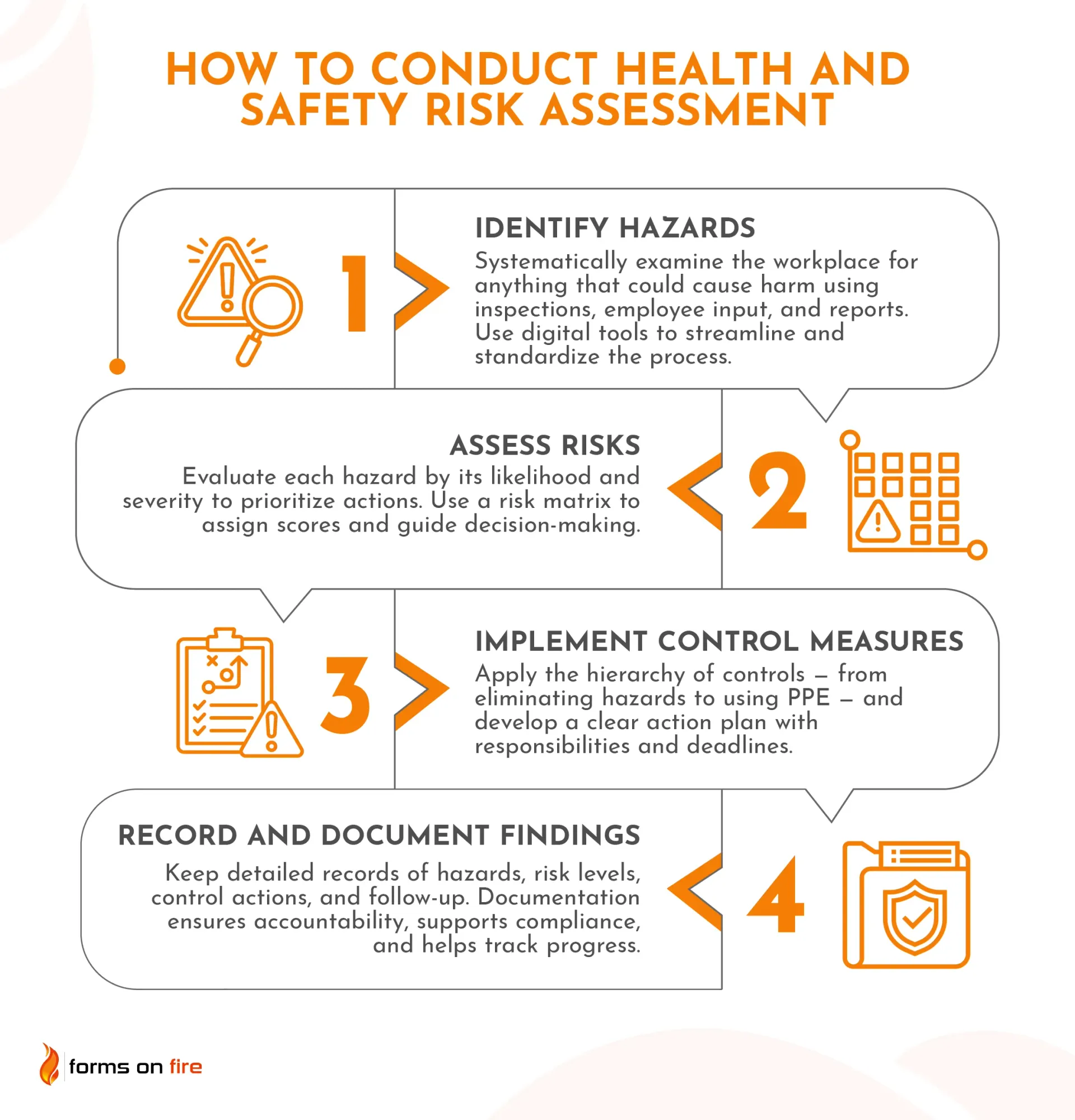
Step 1: Identify hazards
Start by systematically looking for anything that could potentially cause harm. Hazards generally fall into several categories you can see in the image below.
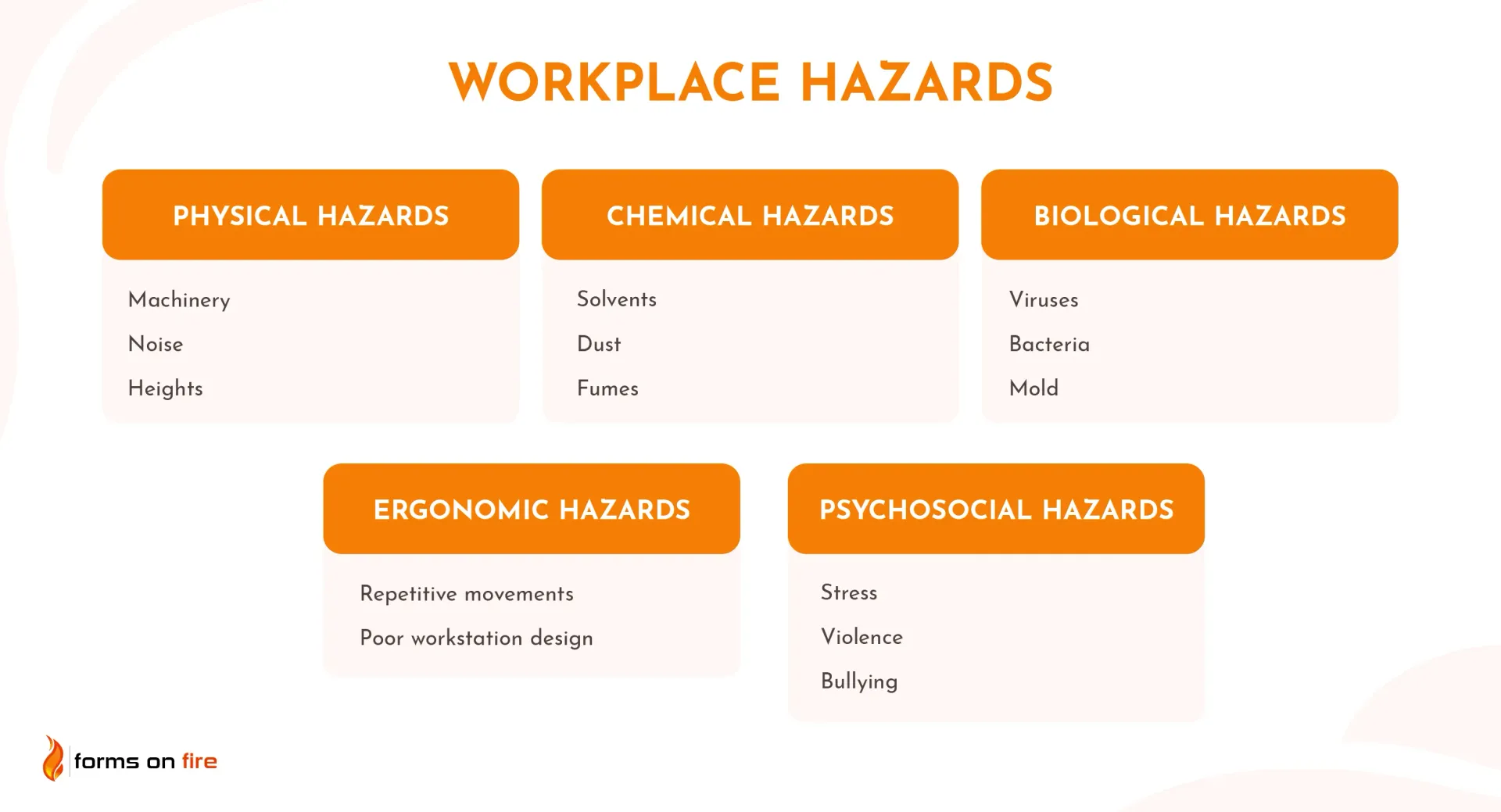
Use multiple methods to ensure thorough identification:
- Workplace inspections let you observe conditions and practices directly.
- Employee interviews provide insights from those who do the job daily.
- Reviewing incident reports to spot recurring issues caused by weak procedures, faulty equipment, and careless or insufficiently trained employees.
- Checking industry guidelines to see common hazards you should watch for in your specific sector.
Mobile forms software like Forms On Fire can dramatically improve this process. Instead of juggling paper forms, you can use customized digital checklists that guide inspectors through each area, capture hazard photos, record employee input, and ensure consistent data collection. This way, nothing gets missed, and it’s easier to compare the findings across departments or periods.
Step 2: Assess risks
Once you've identified your hazards, evaluate each one to determine its risk level. Consider two key factors: how likely it is to cause harm and how severe that harm could be.
A classic risk assessment matrix helps standardize this process. For example, you might rate likelihood from 1 (rare) to 4 (almost certain) and severity from 1 (minor injury) to 4 (fatality). Multiplying these values gives you a risk score that helps prioritize your response.
Let’s go over the example from a manufacturing plant:
LIKELIHOOD / SEVERITY | LOW (1) | MEDIUM (2) | CRITICAL (3) | DISASTROUS (4) |
---|---|---|---|---|
DEFINITELY (4) | 🟨 4 Slips/trips on clean floors | 🟧 8 Excessive noise exposure | 🟥 12 Improper lockout/tagout | 🟥 16 Unguarded machinery with exposed moving parts |
LIKELY (3) | 🟩 3 Minor strains from occasional lifting | 🟨 6 Chemical splashes during transfers, repetitive motion injuries | 🟧 9 Forklift collisions in busy aisles, falling objects from storage racks | 🟥 12 Fire hazards from flammable material storage |
POSSIBLE (2) | 🟩 2 Minor cuts or bruises from hand tools | 🟨 4 Exposure to welding fumes, improper manual handling | 🟨 6 Falls from loading docks | 🟧 8 Electrical shock from damaged equipment |
RARE (1) | 🟩 1 Paper cuts in the office area | 🟩 2 Skin irritation from mild cleaners | 🟩 3 Eye strain from computer work | 🟨 4 Structural failure of storage shelving |
Color key:
- 🟩 Acceptable (1-3): These risks are generally manageable with existing controls. Regular monitoring is sufficient, and work can continue normally.
- 🟨 Tolerable (4-6): These risks require attention but aren't urgent emergencies. You should implement additional controls within a reasonable timeframe and monitor the situation more closely.
- 🟧 Considerable (8-9): These risks demand prompt action. They should be high on your priority list, requiring specific control measures to be implemented without delay. You may need to modify work procedures or add engineering controls.
- 🟥 Intolerable (12-16): These risks require immediate intervention. Work activities may need to stop until adequate controls are implemented. These represent critical safety issues that could result in serious injuries, fatalities, or catastrophic outcomes.
These risk assessments shouldn’t be guesswork. Use incident data, employee experience, manufacturer information, and industry statistics to make informed judgments about likelihood and severity.
Step 3: Implement control measures
Once you've identified and assessed risks, it's time to control them using the hierarchy of hazard controls — a systematic approach that starts with the most effective methods and works down:
- Elimination: Completely remove the hazard from the workplace. For example, redesigning a production process to eliminate the need for a hazardous chemical.
- Substitution: Replace the hazard with something less dangerous. This might mean switching from a toxic cleaning solvent to a safer alternative with similar effectiveness.
- Engineering controls: Add physical safeguards that separate workers from hazards. Installing machine guards, ventilation systems, or noise barriers are common ways to reduce risk without relying on worker behavior.
- Administrative controls: Change how people work through procedures, training, and work schedules. For instance, implement job rotation to limit exposure time to vibration or noise, or create standard procedures for handling chemicals.
- Personal Protective Equipment (PPE): Providing protective gear is your last line of defense. This includes hard hats, safety glasses, gloves, and respirators when other methods can't adequately control hazards.
Develop a practical action plan that outlines specific control measures, who's responsible for implementation, and clear deadlines.
For example, your health and safety assessment identified unguarded machinery as a high risk. In that case, your action plan might assign your maintenance supervisor to install appropriate guards within one week, the safety officer to develop updated operating procedures within two weeks, and the training manager to conduct operator training by month's end.
Step 4: Record and document findings
Documenting your risk assessment creates accountability, establishes a baseline for future comparisons, and provides evidence of due diligence. A thorough risk assessment report should include:
- Identified hazards
- Risk evaluations
- Recommended control measures
- Implementation timelines and responsible parties
- Verification methods
Your documentation should cover the assessment process itself, decisions made, actions taken, and ongoing monitoring plans. Use clear language and include supporting evidence like photographs, test results, or employee quotes that influenced your conclusions.
Many jurisdictions have specific legal requirements for risk assessment documentation. While requirements vary, maintaining detailed records is essential for demonstrating compliance. In the US, OSHA requires employers to verify in writing that workplace hazard assessments have been performed, including the date and the person certifying the assessment.
Some industries face stricter requirements — for instance, facilities handling chemicals under EPA regulations need extensive documentation of hazard identification and exposure assessment.
To be sure, check your local regulations and keep records for the required period (typically 3-5 years, but sometimes longer for hazards with delayed health effects).
Examples of health and safety risk assessments
To wrap things up, here are some assessment examples that showcase how different workplaces systematically identify and address their unique hazards:
- The garage manager assessed risks in their repair shop. They identified hazards like toxic fumes, fire risks, electrical shocks, heavy lifting, and moving vehicles. Safety measures, like protective gear and regular inspections, were already in place, but they added more training and emergency drills.
- A maintenance manager assessed risks in a factory, checking for hazards in both their small workshop and across the facility. Key risks included unfamiliar contractors, heavy machinery, vehicle traffic, and working at heights. Safety measures like clear site procedures, protective gear, and regular inspections were already in place, but they also introduced contractor training and stricter supervision.
- A lab safety plan for Jo Bruin Lab ensures researchers stay safe while working with hazardous materials, nanotechnology, and chemicals. Risks include fire hazards, toxic exposure, and electrical safety. Existing precautions include safety training, proper storage, and regular inspections. Additional steps, like improved protective equipment and emergency response planning, keep risks manageable.
All three examples follow the same effective methodology: identifying hazards, evaluating existing controls, determining risk levels, and implementing additional safeguards where needed.
Improve workplace safety with Forms On Fire
Managing workplace risks effectively requires the right tools, and Forms On Fire simplifies the entire process. This powerful digital platform helps businesses streamline safety inspections, automate risk assessments, and ensure compliance — without the hassle of paperwork.
With mobile-friendly checklists, data collection forms that work online and offline, and seamless reporting, Forms On Fire makes it easier to track hazards, document safety measures, and take immediate corrective action.
Want to learn more?
- See how Forms On Fire simplifies EHS management
- See how Forms On Fire simplifies Risk Management and Compliance
Whether you're in manufacturing, healthcare, construction, or any other industry, we will help you stay proactive about workplace safety.