How to Track and Ensure Safety Compliance
In the U.S. alone, private industry employers reported over 2.8 million nonfatal workplace injuries and illnesses in 2022. And that doesn’t even account for the human and financial toll of serious incidents or fatalities.
Furthermore, failing to comply with safety regulations can lead to steep fines, lawsuits, damaged reputation, and worst of all, preventable harm to employees. That’s why staying on top of safety compliance isn’t optional — it’s essential.
Whether you’re a compliance manager, operations lead, or safety officer, we will share practical tips on tracking and enforcing safety compliance — from choosing the right tools to creating a culture of accountability.
Understanding safety compliance
Workplace safety compliance means following all applicable safety laws, regulations, and internal protocols to protect workers from harm. It’s not just about avoiding fines — it’s about ensuring everyone goes home safe at the end of the day.
Here are some key regulations and standards to know:
- OSHA (Occupational Safety and Health Administration): U.S. agency that sets and enforces workplace safety standards.
- ISO 45001: An international standard for occupational health and safety management systems.
- NFPA (National Fire Protection Association): Sets standards for fire prevention and electrical safety.
- EPA Regulations: Rules covering environmental hazards in the workplace.
- DOT Regulations: For businesses with commercial vehicles or transport operations.
Naturally, not all industries have the same risks or rules. For example:
- Construction deals with fall hazards, heavy machinery, and PPE requirements.
- Healthcare must manage biological risks, patient handling, and infection control.
- Manufacturing often focuses on machine guarding, lockout/tagout procedures, and chemical safety.
- Oil & Gas must follow stricter environmental and emergency response protocols.
Knowing which standards apply to your industry is the first step to staying compliant — and staying safe.
The scope of safety compliance management
Safety compliance management should focus on building a system that keeps safety front and center in daily operations. This means having the right policies, processes, and tools in place to prevent incidents and respond when things go wrong.
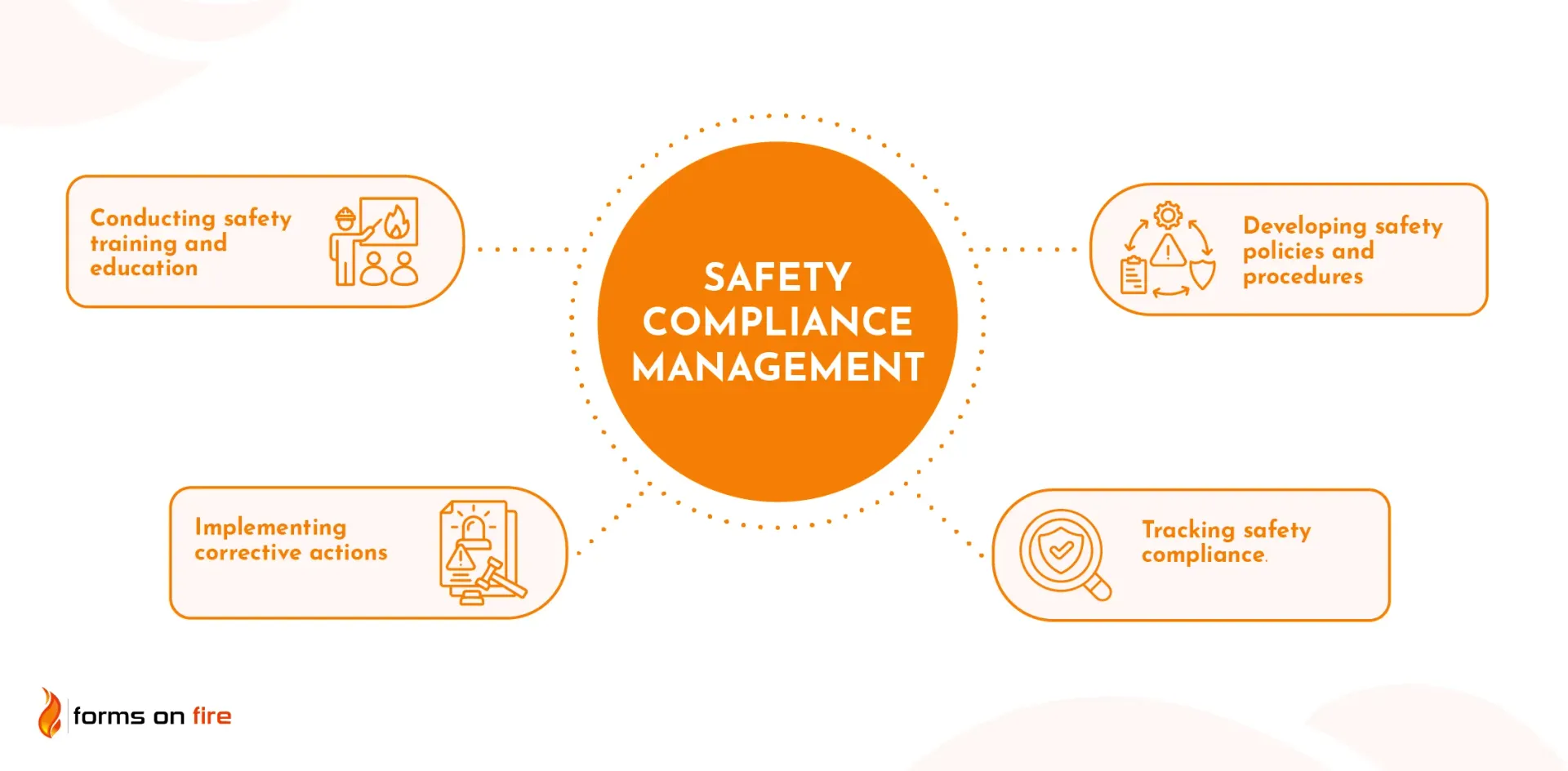
This typically involves:
- Policy development: Setting clear safety standards and expectations for your team.
- Monitoring: Regularly checking that safety practices are being followed.
- Enforcement: Taking corrective action when there’s a violation.
- Training: Making sure employees understand and can apply safety procedures.
In general, there are two layers of responsibilities: internal and external. Internal safety compliance means meeting your company’s own safety policies and procedures. External safety compliance is about following laws, regulations, and industry standards.
Lastly, safety compliance shouldn’t live in a silo. It needs to be aligned with your overall risk management plan, EHS program, and even your day-to-day operations. Managing safety effectively is much easier when treated as part of the business strategy.
Tools for tracking safety compliance
Digital tools are becoming more prevalent in safety management, especially in large organizations. They make it easier to stay organized, spot issues early, and keep everything in one place.
There are two common approaches to digitizing safety and compliance processes:
- Off-the-shelf compliance software: Tools built specifically for EHS or compliance management (like SafetyCulture and EHS Insight). They come with templates, dashboards, and built-in workflows — great if your needs are standard and you want to get up and running quickly.
- No-code platforms: These let you build custom forms, workflows, and dashboards without needing to write code (like Forms On Fire). Perfect if your safety procedures are unique, you want full control over how things are tracked, or want to start slow and digitalize just a few processes.
Both approaches allow you to keep all your checklists, incident report forms, training logs, and inspection forms in one digital hub — easily searchable, shareable, and backed up. This makes it easier to prepare for audits, track trends over time, and stay compliant.
Tracking safety performance is only useful if you're measuring the right things. As a safety manager, you want KPIs that align with your goals, risks, and regulatory requirements.
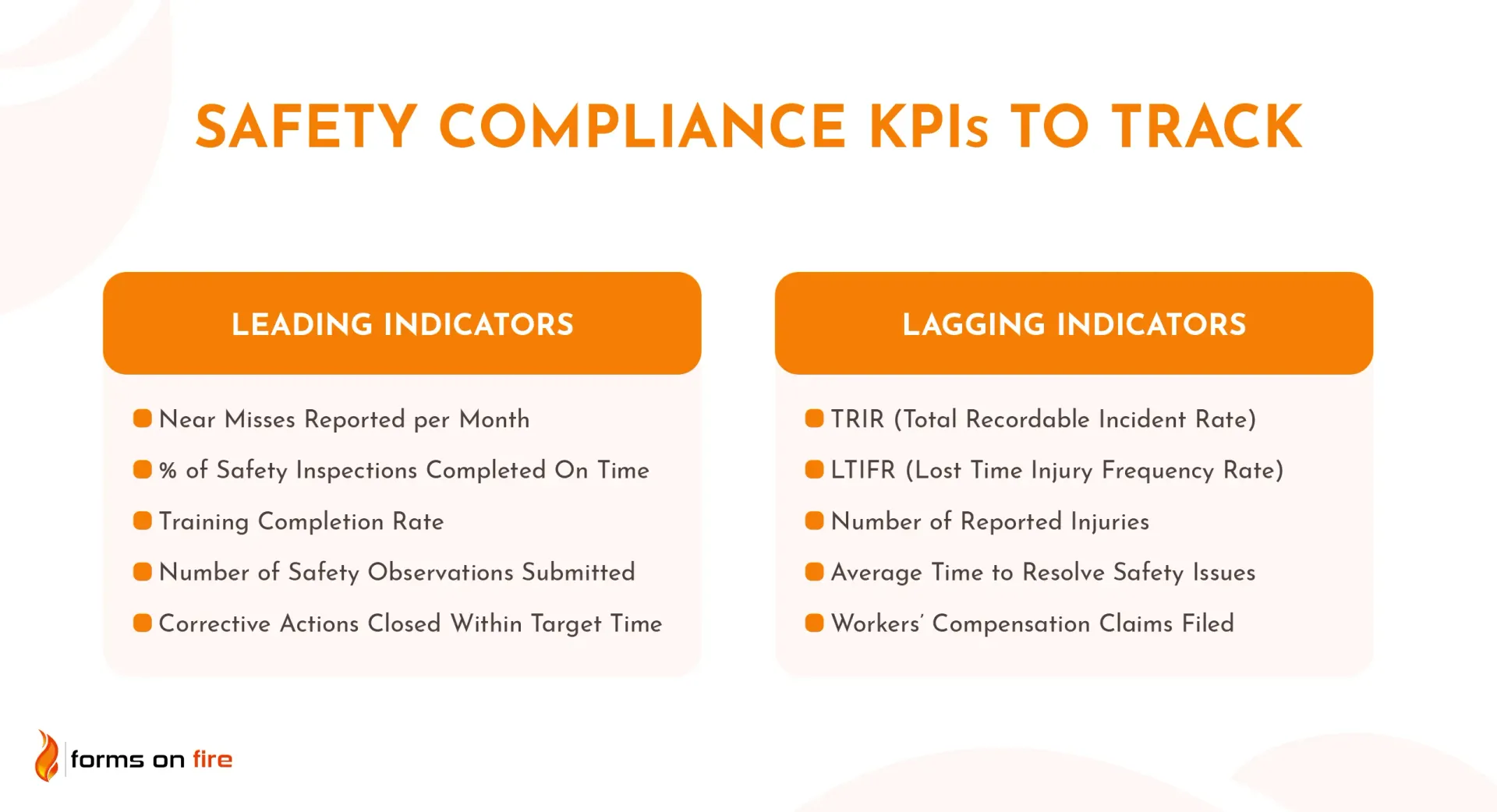
Here’s how to choose the right metrics:
- Start with your biggest risks: What’s most likely to cause harm in your workplace? For example, if you’re in construction, you might focus on fall incidents. In manufacturing, it might be equipment-related injuries.
- Map KPIs to your compliance requirements: Are there regulatory targets you need to meet (e.g., OSHA recordables)? If so, your KPIs should help you track and prove that compliance.
- Choose both leading and lagging indicators: Lagging indicators show what’s already happened — like TRIR or number of incidents reported. Leading indicators help you catch issues early — like number of safety trainings completed or near misses reported.
- Keep it simple and actionable: Don’t track 20 KPIs if you only have time to act on 5. Focus on metrics you can monitor regularly and actually use to make improvements.
These should give you a clear picture of both your current safety culture and potential blind spots.
Ways to enforce and ensure workplace safety compliance
Having safety policies is one thing — making sure people follow them is another. This section walks through five strategies every safety manager should use to make compliance stick — not just during inspections, but every day on the job.
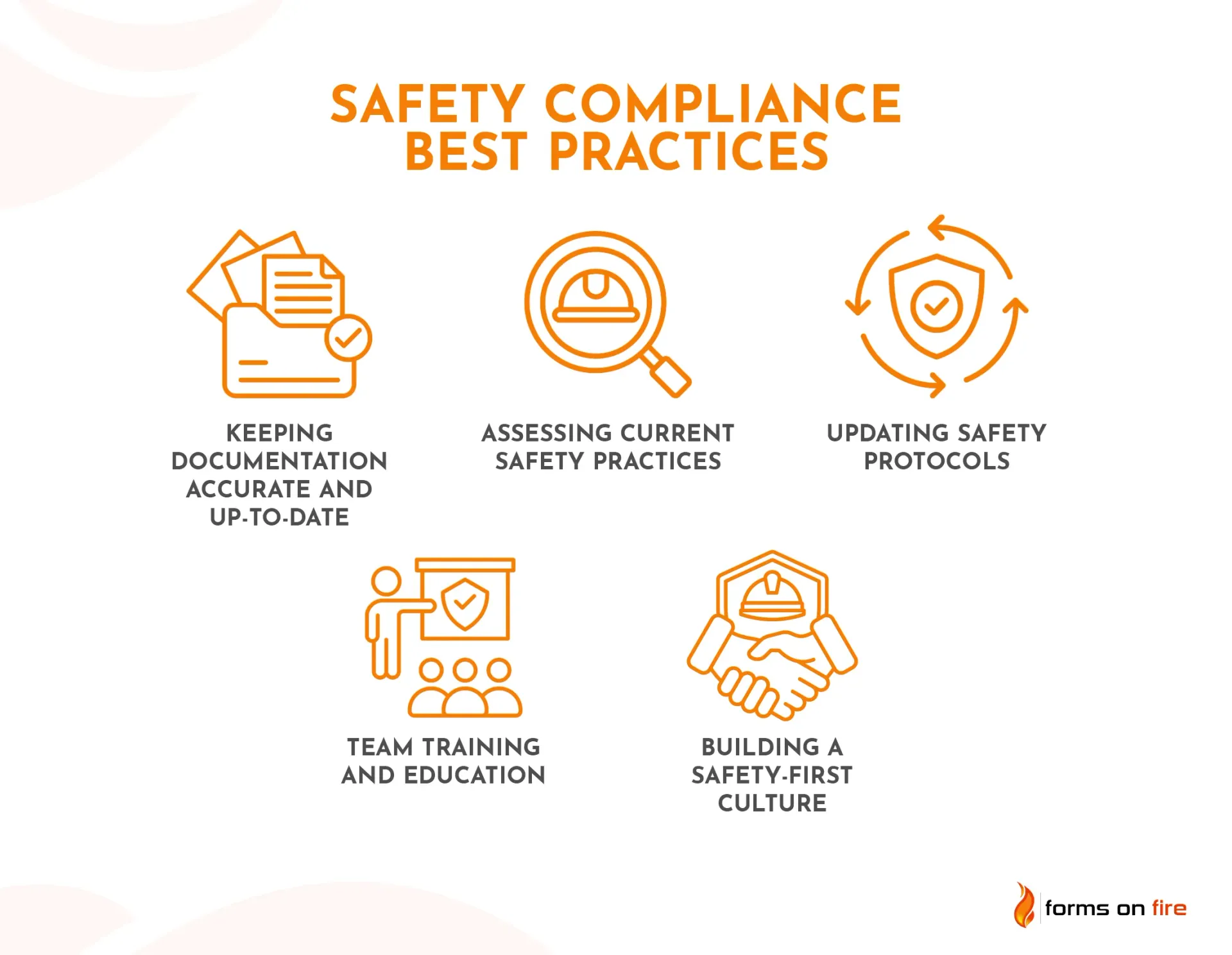
1) Keeping documentation accurate and up-to-date
Good documentation is your best defense in a safety audit — and your best tool for preventing repeat incidents. If it’s missing, outdated, or inconsistent, you’re putting your team (and your company) at risk.
Regulators often ask for inspection logs, incident reports, and training records during audits. Up-to-date documentation shows that your safety program is active and taken seriously.
Here are quick tips to keep safety documentation in check:
- Go digital: Paper gets lost. Use digital tools to log incidents, track inspections, and store everything in one place.
- Use standardized forms and checklists: Create templates for things like incident reports and safety inspections. Easily collect any type of safety data you need.
- Make it real-time: Get supervisors and employees to log issues on-site using mobile devices. The faster the data is recorded, the more accurate it will be.
- Set regular review cycles: Schedule quarterly or yearly reviews to clean up old data, check for missing reports, and update procedures as needed.
2) Assessing current safety practices
Regularly assessing your current safety practices helps identify compliance gaps before they become real problems.
The most effective way to do this is to:
- Conduct safety audits: These should be done routinely — not just when something goes wrong. Audits can be internal or external and should cover everything from equipment inspections to PPE usage and employee behavior.
- Review incident reports and near misses: Don’t just file them away. Analyze trends. Are similar incidents happening in the same area or shift? Are near misses increasing? These patterns will tell you where attention is needed.
- Use checklists and walkthroughs: Walk the floor, talk to employees, and use structured checklists to catch the small stuff that might be missed in day-to-day operations.
- Evaluate safety culture: Are employees comfortable reporting hazards and near misses? Are supervisors leading by example? A culture check might be just as important as a clipboard check.
Recurring health and safety risk assessments and audits keep safety efforts grounded in reality — not just rooted in a broadly or vaguely defined policy.
3) Updating safety protocols
New equipment, new profile of workers, changing industry guidelines, an increased number of incidents reported — there are plenty of reasons to review and update your safety protocols.
Here’s how to stay on top of it:
- Revise policies after incidents or audits:
If an audit reveals a gap or an incident exposes a weak spot, update your policies to address it. Don’t wait until the next scheduled review.
- Create or revise Standard Operating Procedures: SOPs often include a safety components. They should be written in plain language and easy to access on the job site (digital helps here, too).
- Communicate changes clearly: Updates don’t matter if no one knows about them. Use toolbox talks, training sessions, or team meetings to explain what’s new and why it matters.
- Assign accountability: Make sure someone owns each safety KPI, protocol update, or audit follow-up. When responsibility is clear, things are more likely to get done.
4) Team training and education
It is hard to talk about safety compliance without mentioning the importance of employee education. Training ensures they know how to stay safe, what’s expected of them, and how to react when something goes wrong.
Safety training must be part of the onboarding process, followed by regular refreshers.
From in-person sessions and online modules to drills and simulations, there are various training methods you can use. Ideally, you are able to mix and match these methods depending on your team, industry, and work environment. Try to make compliance training fun to improve retention.
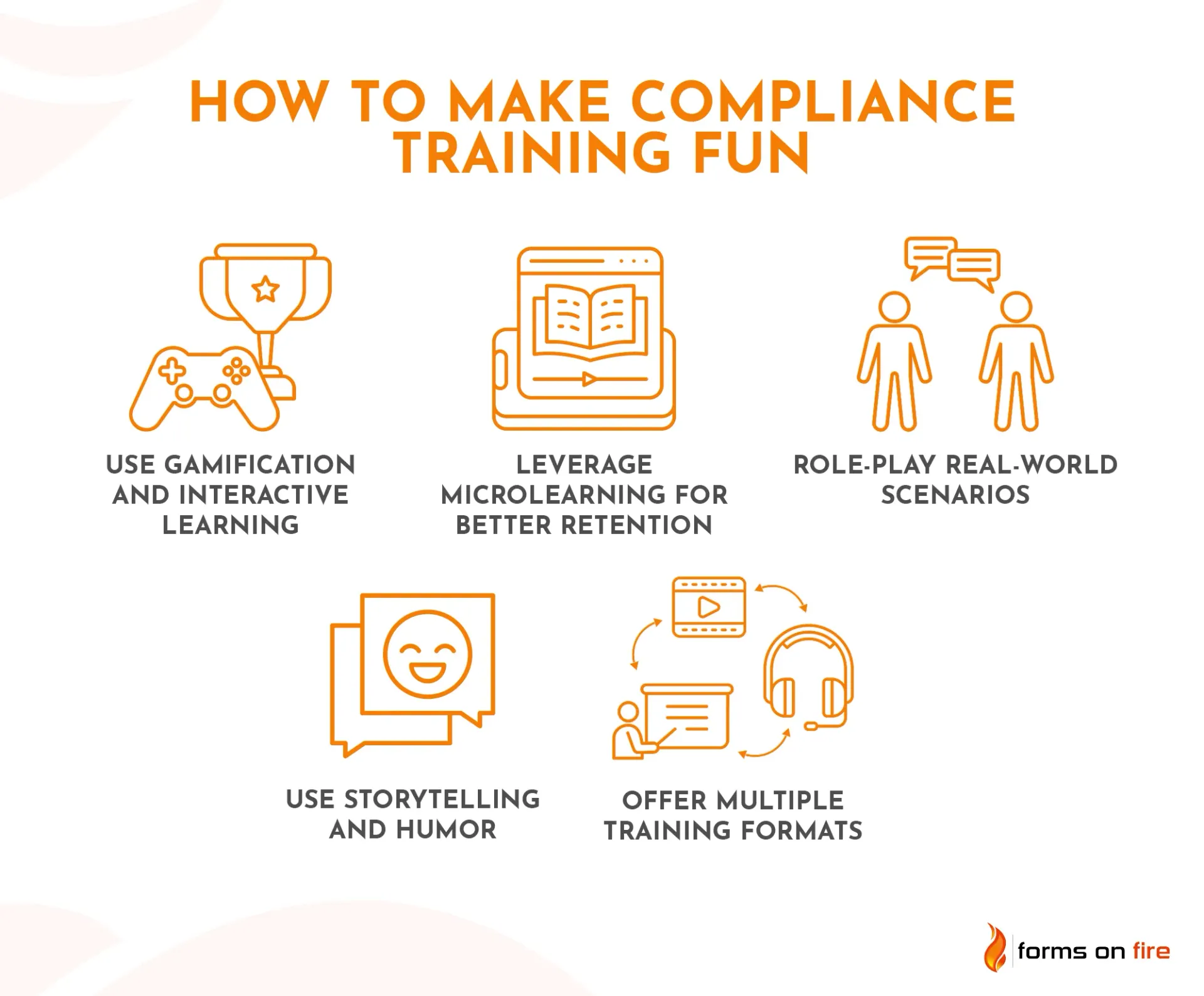
5) Building a safety-first culture
Culture is what turns rules into habits — it’s the difference between compliance because you have to and safety because your team wants to.
This is a topic that is covered ad nauseam. There are various guides, lessons, and videos you can find that dive deeper into this theme. Most of them boil down to these three concepts:
- Leadership commitment: Safety starts at the top. If leaders don’t walk the talk, employees won’t either. Managers should be the first to wear PPE, report hazards, and show that safety is a priority — not an afterthought.
- Employee involvement: Frontline workers are the eyes and ears of your operation. Give them a voice. Encourage hazard reporting, involve them in safety committees, and ask for feedback on protocols that may not work in the real world.
- Recognition and incentives: Don’t just highlight what went wrong — celebrate what’s going right. Recognize safe behavior in meetings, offer small rewards for reporting near misses, and make people feel like safety wins are team wins.
A safety-first culture takes time, but once it’s in place, everything else — training, compliance, inspections — gets easier.
Simplify safety compliance management with Forms On Fire
Forms On Fire is a no-code platform that helps organizations digitize and streamline their internal processes — without needing a full IT team or complex software rollouts.
Instead of juggling paper forms, spreadsheets, or clunky systems, Forms On Fire lets you build custom safety checklists, incident report forms, and inspection workflows in one simple app. You can assign tasks, upload photos, collect signatures, and generate reports — all from a phone or tablet.
Here’s how it helps with safety compliance:
- Hundreds of templates you can use to quickly build custom, mobile-friendly forms for inspections, audits, incident reports, training, SOPs, etc.
- Real-time data sync so nothing gets lost or forgotten.
- Offline mode for teams working in remote or low-connectivity environments.
- Custom dashboards to track safety KPIs and trends.
- Automated workflows to assign work, track progress, follow-up, and notify the right people.
- Dedicated support team that will guide you through the whole process, from creating safety forms to deploying them.
- And much more.
Seeing is believing, so we invite you to schedule a quick product demo. Tell our team what you need, and they will show you how Forms On Fire can help!