A Crash Course to EHS Compliance Management
EHS compliance is a critical part of running a responsible, efficient, and safe organization. For industries like manufacturing, construction, healthcare, and utilities, it’s the backbone of protecting employees, the environment, and your business reputation. But even sectors like retail and tech aren’t exempt from the need to manage compliance effectively.
In this article, we’re diving into everything you need to know about EHS compliance management — from understanding what it covers and why it matters to breaking down the key components of an effective program.
Let’s start with a quick definition.
What is EHS compliance?
EHS compliance stands for Environment, Health, and Safety compliance. It refers to a company’s adherence to regulations, standards, and best practices aimed at protecting the environment, ensuring workplace safety, and safeguarding the health of employees.
Essentially, it’s about creating a safe and sustainable work environment while staying on the right side of the law.
Companies pay a lot of attention to EHS compliance because of:
- Legal implications: Non-compliance with EHS regulations can lead to hefty fines, lawsuits, and even criminal charges in severe cases. For instance, failing to follow OSHA guidelines or EPA standards can result in penalties that not only hurt your bottom line but also damage your ability to operate.
- Financial risks and reputational damage: Beyond fines, EHS violations can lead to costly downtime, damaged assets, and increased insurance premiums. Plus, in today’s socially conscious world, news of an environmental or safety mishap can quickly spread, tarnishing your brand’s reputation with customers, investors, and the public.
- Employee well-being and environmental sustainability: EHS compliance ensures your employees feel safe and valued, reducing accidents and improving morale. On a broader scale, it helps minimize your organization’s environmental footprint.
Now that we have the basics down, let’s explore the key components of an effective EHS compliance management system.
Key components of EHS compliance management
How complex your EHS compliance management will mainly depend on the industry you operate in and how large your organization is.
In general, a comprehensive EHS compliance program needs to cover everything from understanding regulations to training employees, assessing risks, and continuously improving processes.
Let us dive deeper into each of its components so we can get more practical.
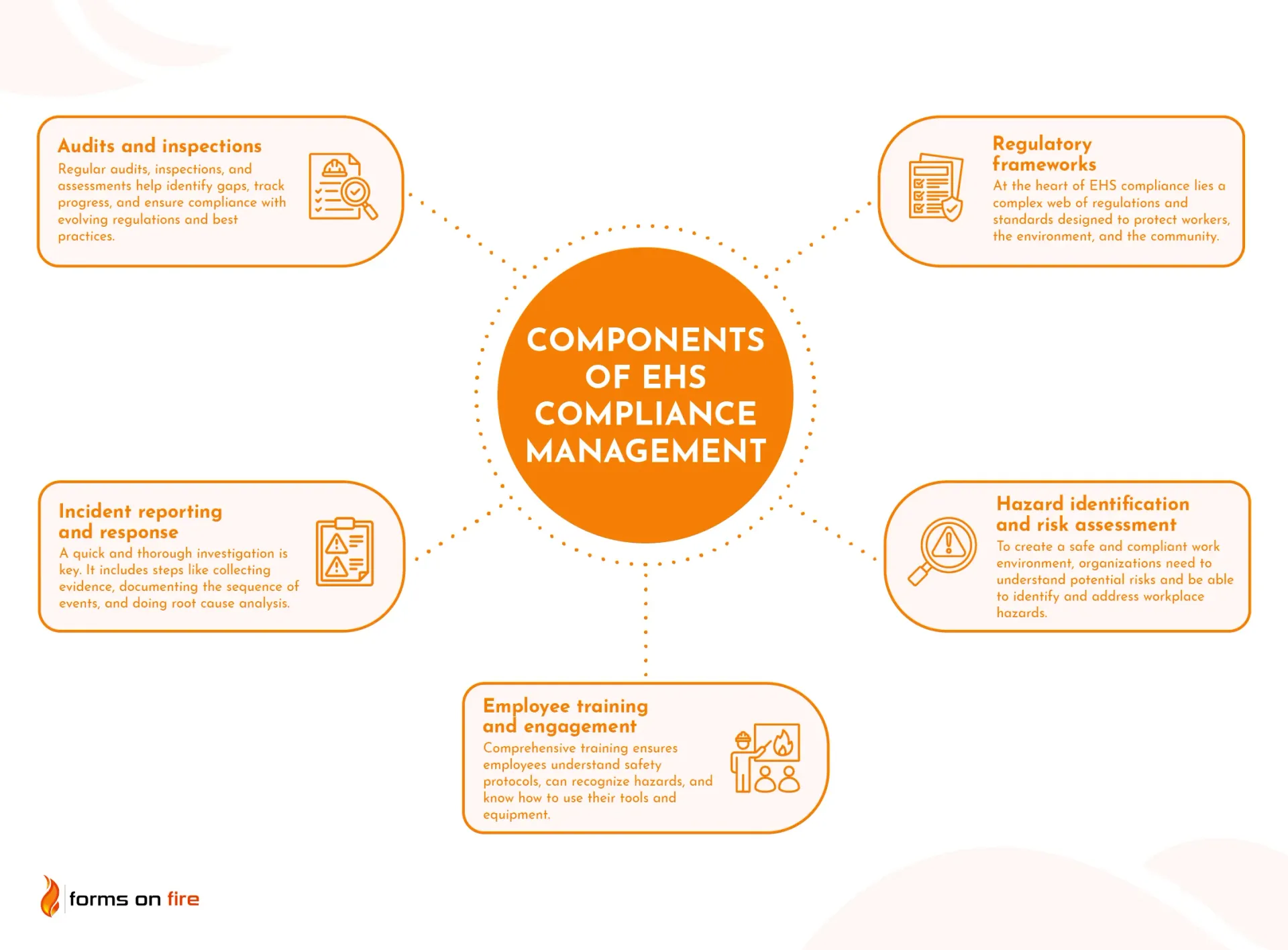
1) Regulatory frameworks
At the heart of EHS compliance lies a complex web of regulations and standards designed to protect workers, the environment, and the community. These frameworks provide the rules and guidelines organizations must follow to stay compliant.
Some of the key regulations and standards include:
- OSHA: Focuses on workplace safety and employee health in the U.S.
- EPA: Governs environmental regulations, such as air quality, water safety, and hazardous waste.
- ISO 14001: An international standard for environmental management systems.
- ISO 45001: Focuses on occupational health and safety management.
If you operate internationally, you know that regulatory requirements vary significantly by region. It is imperative to know the specifics of each of the locations you operate in. For example:
- In the U.S., OSHA and EPA set stringent rules for workplace safety and environmental protection.
- The EU enforces regulations like REACH (Registration, Evaluation, Authorization, and Restriction of Chemicals) and stringent workplace safety directives.
- Canada focuses on compliance through organizations like Environment and Climate Change Canada (ECCC) and provincial safety standards.
Navigating these regulatory frameworks can be complex — which is why you need to stay informed and proactive.
2) Hazard identification and risk assessment
Identifying and addressing workplace hazards is a cornerstone of EHS compliance management. Without a clear understanding of potential risks, it’s impossible to create a safe and compliant work environment.
Hazards in the workplace can come in many forms, including:
- Chemical hazards: Exposure to harmful substances like solvents, acids, or toxic gases.
- Physical hazards: Noise, extreme temperatures, or unsafe equipment.
- Biological hazards: Pathogens, mold, or exposure to infectious materials.
Conducting regular inspections and keeping communication open with employees are critical steps to uncovering these risks.
Another great way to get in front of issues is to conduct regular risk assessments. They help evaluate the likelihood and severity of hazards, providing a clear roadmap for managing them. Popular methods include Job Safety Analysis (JSA), Hazard and Operability Study (HAZOP), and Quantitative Risk Assessment (QRA).
Once you know which hazards you’re dealing with and how much risk they bring, it’s time to put some control measures in place. You can do that by following this simple hierarchy of controls:
- Elimination: Remove the hazard entirely.
- Substitution: Replace hazardous materials or processes with safer alternatives.
- Engineering controls: Isolate hazards with barriers or ventilation.
- Administrative controls: Update work procedures, provide training, or limit exposure time.
- Personal Protective Equipment (PPE): Use gloves, goggles, or respirators as a last line of defense.
3) Employee training and engagement
If using PPE is the last, a well-informed workforce is your first line of defense against risks and regulatory violations.
Comprehensive training ensures employees understand safety protocols, can recognize hazards, and know how to use their tools and equipment. Training should be an ongoing process — not a one-time event — to account for new regulations, procedures, tools, and technologies.
While necessary, EHS guidelines often complicate and slow down daily operations, especially for frontline workers. If you want everyone to follow those guidelines, you will need to develop a strong EHS culture. You can do that by:
- Leading by example: Managers and leaders must demonstrate a commitment to EHS principles.
- Encouraging open communication: Foster an environment where employees feel comfortable reporting hazards or sharing concerns.
- Recognizing contributions: Celebrate employees who uphold safety practices and contribute to a safer workplace.
Before we move on, let us also note that proper documentation of training programs, employee certifications, and safety procedures isn’t just a best practice — it’s often required by law. Keep detailed records so you can demonstrate compliance during audits.
4) Incident reporting and response
Despite your best efforts, it’s almost impossible to eliminate incidents entirely. What sets great organizations apart is how they respond.
When an incident occurs, a quick and thorough investigation is key. It includes steps like collecting evidence (photos, witness statements, equipment logs…) and documenting the sequence of events leading up to the incident.
Do yourself a favor and standardize this process as much as possible. The easiest way to do that is to use an incident report form template that covers the 5W’s you can see in the image below.
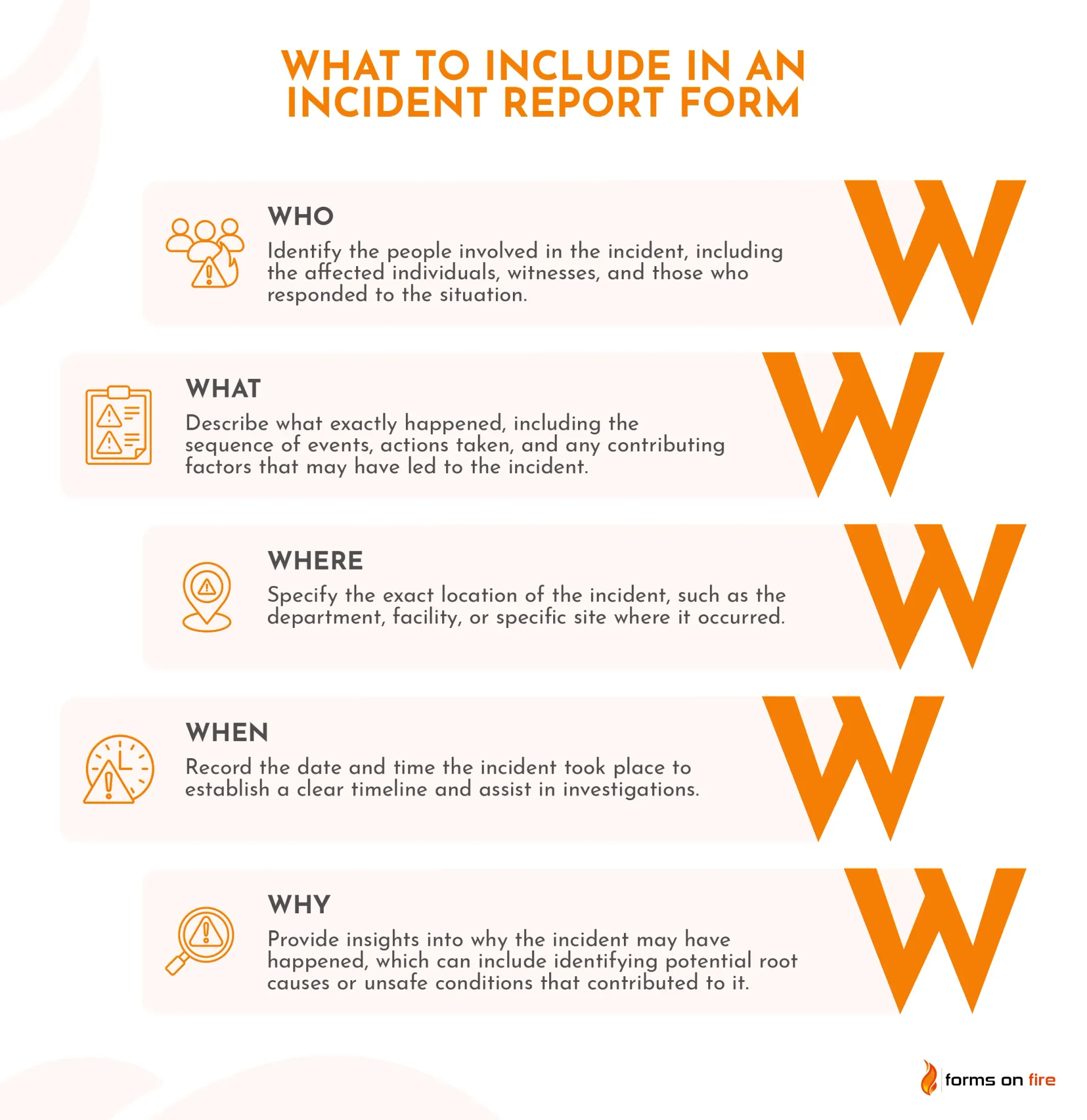
After an incident, use techniques such as Fishbone Diagrams, Failure Mode and Effects Analysis, and the "5 Whys" to identify the root causes. This is the only way to implement corrective actions that will actually prevent recurrence.
Last but not least, effective EHS compliance management also includes the creation of an emergency preparedness plan. In it, consider including things like:
- Evacuation procedures and assembly points.
- Contact lists for emergency services and key personnel.
- Communication protocols to inform employees and stakeholders.
- Regular drills to ensure everyone knows what to do in a crisis.
As the saying goes, it’s better to be safe than sorry.
5) Audits and inspections
Regular audits, inspections, and assessments are essential for maintaining EHS compliance. They help identify gaps, track progress, and ensure your organization stays aligned with evolving regulations and best practices.
The audits can be performed internally or externally. You can see the difference between the two in the table below.
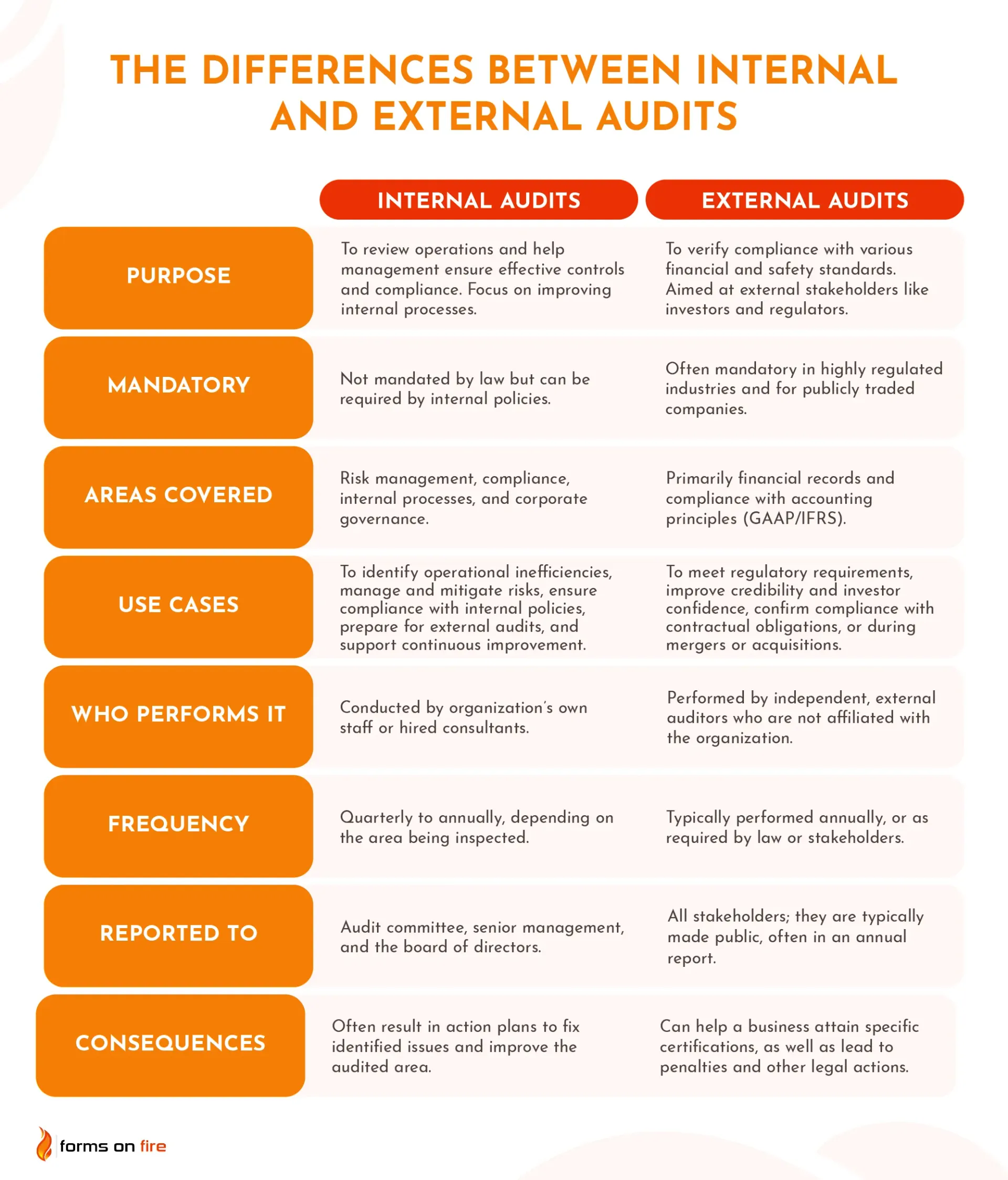
If you plan to conduct internal audits regularly — which you should — you’ll want to standardize the process as much as possible.
You can use a no-code forms builder like Forms On Fire to create digital checklists your audit team can follow while performing specific inspections and collecting data. If you digitize the process this way, you will have a wat easier time updating procedures, tracking compliance metrics, and generating compliance reports on demand.
Lastly, don’t use inspections and audits just as a tool to identify problems — they’re opportunities to improve. An effective EHS compliance management means following up on findings with actionable steps, such as :
- Updating policies and procedures to address gaps.
- Providing additional training for employees.
- Investing in new technologies or equipment to enhance safety and efficiency.
That is how you create a culture of accountability and continuous improvement.
Simplify EHS compliance management with Forms On Fire
Forms On Fire is a no-code platform that organizations you to build everything from simple checklists and data collection forms to customized compliance management solutions.
Forms On Fire helps companies:
- Streamline data collection: Whether it’s capturing incident reports, audit checklists, or employee training records, the platform allows you to collect data on the go using smartphones or tablets. Plus, it works offline, so you’re covered even in remote locations.
- Simplify reporting and record-keeping: Staying compliant requires accurate and organized records. Forms On Fire automatically organizes your data and generates professional reports, making it easy to meet regulatory requirements and prepare for audits.
- Boost efficiency and accountability: From automating reminders for inspections to tracking corrective actions, Forms On Fire ensures nothing falls through the cracks. Custom dashboards give you a bird’s-eye view of your compliance metrics, helping you make informed decisions and demonstrate accountability to stakeholders.
To make things easier, we have hundreds of pre-made templates you can choose from. Just pick the form you need and customize it so it fits perfectly into your existing workflows.
The best thing about using Forms On Fire for compliance management is that you can start small — digitizing one or two specific processes — then scale up. You are not constrained by a rigid pre-made solution that forces you to do things in a specific way and has a bunch of features you will never use (but still need to pay for).
Want to see a more practical example of how Forms On Fire can help you streamline EHS compliance management? Book a quick chat with our team or start a 14-day free trial of Forms On Fire.