How to Prepare for and Conduct a Thorough Workplace Safety Audit
Regular safety audits are essential for maintaining a safe workplace, ensuring compliance, and identifying potential hazards before they become real problems.
However, many organizations face challenges when conducting safety audits. Common issues include lack of preparation, difficulty staying impartial, or the process becoming time-consuming and disorganized.
In this article, we’ll walk you through everything you need to know to prepare for and conduct an effective workplace safety audit and overcome common hurdles along the way.
What is a safety audit?
A safety audit is a systematic process designed to evaluate a workplace's safety practices, policies, and procedures. It involves identifying potential hazards, assessing compliance with safety regulations, and determining areas for improving safety practices. It can be performed by external auditors or by an internal team of experts.
There are several important reasons to regularly conduct workplace safety audits:
- Identify hazards: Audits uncover safety risks that may otherwise go unnoticed.
- Ensure compliance: Many government agencies, like OSHA in the U.S., require businesses to meet specific safety standards. Failure to comply with these regulations can lead to fines, penalties, or legal action.
- Prevent incidents: Proactively addressing hazards helps prevent accidents, injuries, and even fatalities.
- Improve efficiency: A safer work environment reduces downtime caused by incidents or non-compliance issues.
- Boost employee confidence: Workers feel safer and more confident when they know their employer prioritizes safety.
Before we move on, we noticed that some managers confuse safety audits with safety inspections. Below is a quick table that outlines the differences.
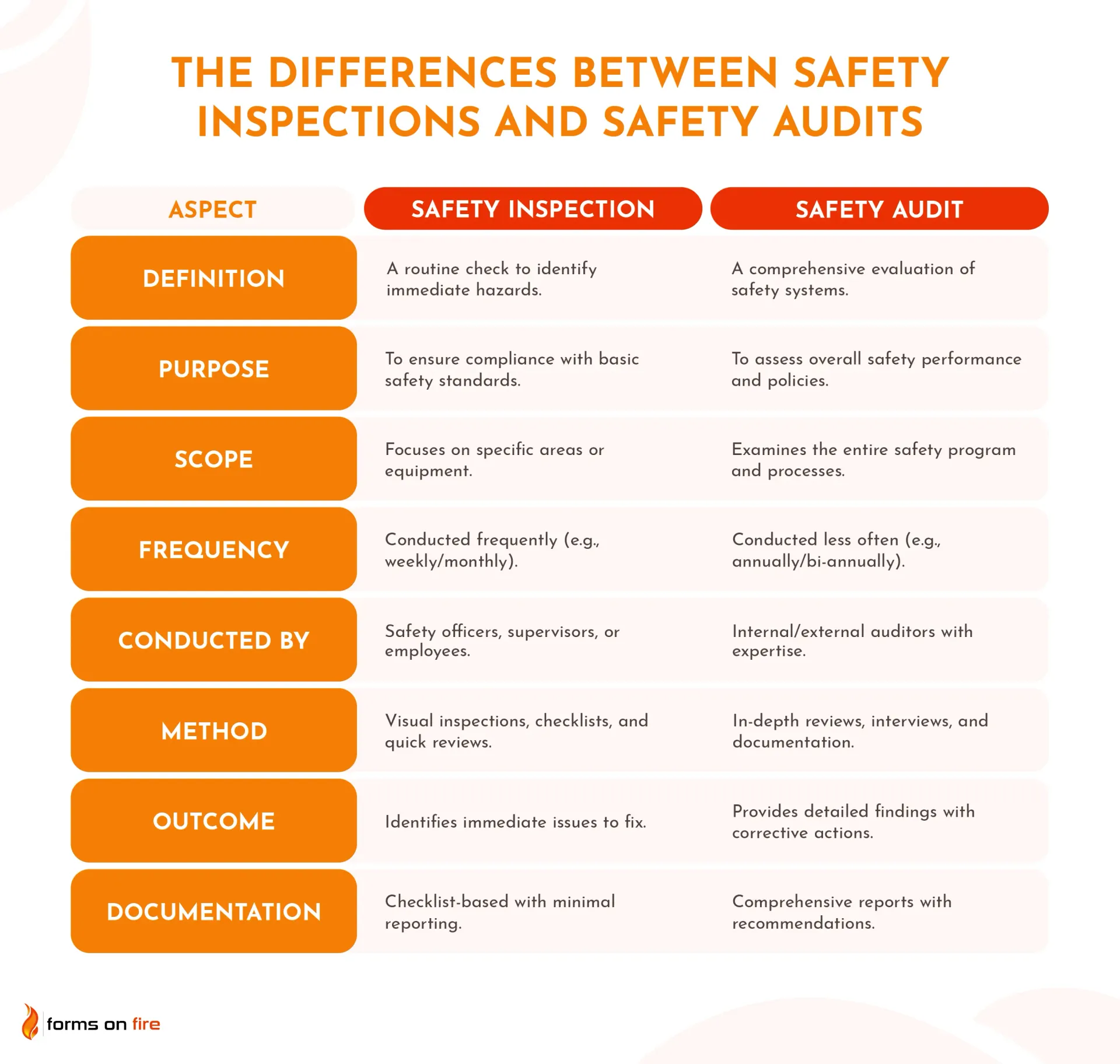
How to conduct a general safety audit
Conducting a workplace safety audit doesn’t have to be complicated, but it does require some planning, impartial execution, and the right tools.
In the following sections, we’ll break down the process into actionable steps that are easy to follow.
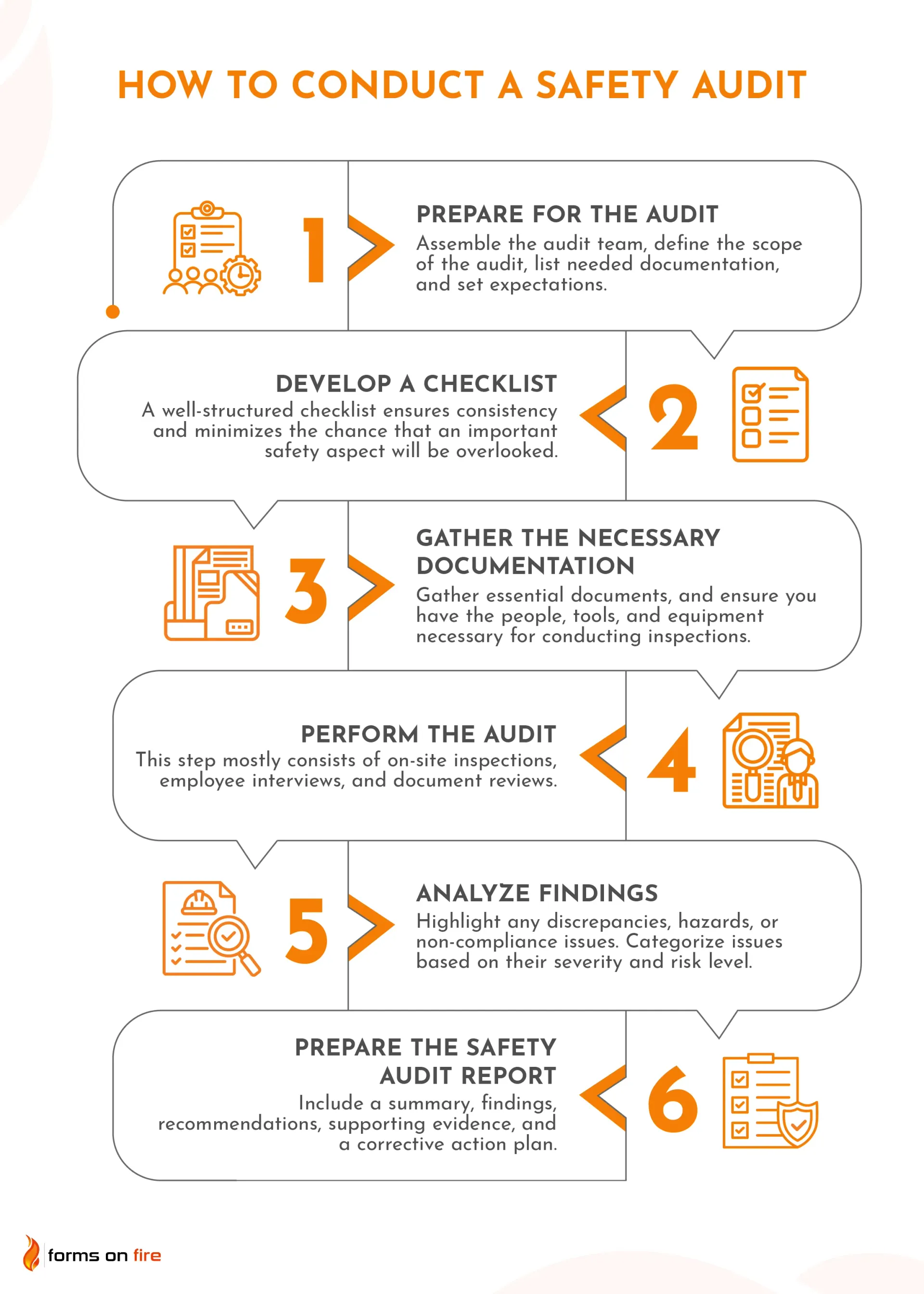
1. Prepare for the audit
Proper planning ensures that the audit runs smoothly and delivers valuable insights. Here’s what you will want to do:
- Assemble the audit team: Select a team of individuals who will conduct the audit. This team should include safety experts, supervisors, and, if possible, individuals who are not directly involved in the areas being audited (to maintain impartiality).
- Define the scope of the audit: Clearly outline the areas, processes, and systems that the audit will cover. Determine the general timeline for the audit — the start date and how long should take to complete it.
- List needed documentation: Think about the documents and records you’ll need for the audit. These may include safety policies, incident reports, inspection records, training logs, and any prior audit findings.
- Set expectations: Communicate the purpose and goals of the audit to the team and relevant stakeholders. Make sure everyone understands their roles and responsibilities during the process.
2. Develop a checklist for your workplace safety audit
A well-structured checklist is almost essential for conducting an effective safety audit. It ensures consistency and minimizes the chance that an important safety aspect will be overlooked.
When building your checklists, focus on the areas most relevant to your organization. Templates you find online can be a great starting point, but be sure to adjust them to reflect your workplace’s specific risks, operations, and compliance requirements.
Here are common items found in a general safety audit checklist:
- Equipment safety: Check for proper functioning, records of regular maintenance, and adherence to safety standards.
- Fire protection systems: Verify fire extinguishers, alarms, and emergency exits are functional and up to code.
- Employee training: Confirm that staff have received adequate training and understand safety procedures.
- Emergency procedures: Ensure evacuation plans, first aid kits, and emergency contact information are current and accessible.
- Industry-specific standards: Include any regulations or guidelines that apply to your industry or operations. For example, a construction business would review its fall protection or scaffolding safety, while a pharmaceutical company would want to inspect its infection control protocols or guidelines for hazardous material handling.
If you are creating a checklist from scratch or want to modernize your paper/Excel checklists, there are plenty of simple form builders like Forms On Fire that can help you do that in minutes. These checklists can be highly customized and used on mobile devices to collect data, streamline inspections, and write down notes and observations. You should also be able to instantly generate reports and maybe even automate some parts of the audit process.
Keep in mind that safety risks evolve as workplaces change — courtesy of new equipment, new people, process changes, and updated regulations. Another big advantage of creating digital checklists is that they are easily adjusted for future safety audits.
3. Gather the necessary documentation and resources
Once your checklist is ready, the next step is to gather all the documentation and resources you will need for the audit. This includes:
- Documentation: Essential documents such as safety manuals, previous inspection records, incident reports, training logs, permits, and maintenance records. These will help you verify compliance and provide a historical perspective on safety practices.
- On-site resources: Ensure you have the tools and equipment necessary for conducting inspections. This can include personal protective equipment (PPE), measuring tools, cameras for documenting findings, and any relevant checklists or audit forms.
- Access to personnel: Coordinate with managers and employees to ensure availability for interviews or clarifications during the audit. Employee insights often uncover hidden risks or gaps in procedures.
Do these steps right, and whoever is responsible for actually conducting the audit will be eternally grateful.
4. Perform the audit
With your checklist and resources in place, it’s time to execute the audit. This stage involves:
- On-site inspections: Walk through the workplace to identify physical hazards, unsafe practices, or non-compliance. Take detailed notes, photos, or videos to document findings.
- Employee interviews: Speak with workers to gain insight into day-to-day safety practices. Ask about their understanding of procedures, concerns they might have, and any incidents that may have gone unreported.
- Document reviews: Compare collected documentation — like inspection logs, training records, and permits — against your checklist and safety standards to identify any discrepancies or gaps.
It is the most time-consuming step, but it’s important to do it right.
Again, you can use mobile tools during this phase to streamline data collection. Digital data collection forms built with Forms On Fire allow auditors to input findings in real time, attach photos, and immediately flag hazards for follow-up — even in places with poor internet access. This ensures accuracy and prevents the loss of critical information during the audit process.
Be thorough but practical during the audit. Focus on identifying systematic issues that directly impact workplace safety and compliance, rather than nitpicking outliers (like an isolated incident that occurred because of a freaky accident or someone consciously deciding not to follow safety guidelines).
5. Analyze findings
Now it’s time to turn the raw data you’ve gathered into meaningful insights that drive safety improvements.
Start by comparing the findings to your checklists. If you are using digital checklists, you should be able to automatically generate reports that highlight any discrepancies, hazards, or non-compliance issues uncovered during the audit.
To make analysis easier, categorize the hazards based on their severity and risk level. For example:
- Critical: Hazards that pose an immediate threat to health or safety and require urgent corrective action. For example, a malfunctioning machine with exposed wiring that could cause electrocution.
- Major: Significant risks that could cause harm if not addressed soon. For instance, employees repeatedly neglecting to wear PPE or an old fire extinguisher that needs to be replaced.
- Minor: Small issues that need improvement but do not pose an immediate risk. Good examples are blocked emergency exists or missing or worn out safety labels.
Prioritizing hazards in this way will help management allocate resources effectively.
6. Prepare the safety audit report
Finally, document the findings clearly and concisely. Here’s how you can organize your safety audit report:
- Summary: Provide a brief overview of the audit’s purpose, key findings, and high-level recommendations.
- Findings: Detail the hazards, non-compliance issues, and other discrepancies identified during the audit. Use charts or tables to present data visually, making it easier for stakeholders to understand the scope of the issues.
- Recommendations: Offer clear, actionable steps to address each issue. Prioritize them based on severity and urgency.
- Supporting evidence: Include photos, charts, and relevant documentation to back up your findings.
- Corrective action plan: Outline rough timelines and responsibilities for addressing each hazard or issue.
Here is a simplified example of an action plan to see how it can look:
Actions to take after your general safety audit
Your audit had a goal — improving workplace safety. That goal can only be achieved by following through with the corrective action.
Regularly check on the status of corrective actions. Schedule follow-up inspections or audits to confirm that issues have been resolved.
For critical and major issues, you should consider putting processes in place to prevent recurrence. Use insights from the audit to update safety policies, training programs, and procedures. Make sure employees are aware of these updates and receive proper training.
Your next workplace safety audit will tell you how successful you have been — so don’t forget to schedule it!
Streamline your audits with simple digital forms
Paper-based audits are prone to human error, inefficiency, and delays in reporting. By switching to digital forms, organizations can significantly boost the accuracy and speed of their safety audits.
Forms On Fire is a no-code app builder that helps managers create all kinds of digital forms and checklists. We have a huge database of different templates (safety included) which you can just pick up and adjust to the operational requirements of your workplace.
If you get stuck, our amazing support team is ready to help. They will help you adjust your forms and make sure they are deployed properly to your mobile devices.
You can learn more by requesting a quick product demo or starting our 14-day free trial.
If you are serious about safety and want to conduct audits regularly, a tool like Forms On Fire will save you a lot of time, money, and nerves.