How to Perform a Quick and Effective Operational Audit
An operational audit serves as your organization's compass for continuous improvement — it helps you examine processes, identify inefficiencies, and uncover opportunities that drive measurable results.
Yet many organizations face critical challenges in their audit processes. They struggle with scattered data collection, reporting, or turning findings into actual improvements.
If you plan to run these audits regularly — which you should — there is a huge benefit in learning how to optimize the operational audit process.
So let’s see how to do just that.
What is an operational audit?
An operational audit is a comprehensive analysis of an organization's internal processes, systems, and controls to evaluate their effectiveness, efficiency, and alignment with business goals.
Unlike financial audits that focus on financial statements and records, operational audits assess how well your business converts resources (inputs) into products or services (outputs).
When conducting an operational audit, you are free to examine every aspect of your operations — from existing workflows and resource allocation to management systems and performance metrics.
Organizations perform operational audits to:
- Identify inefficiencies and bottlenecks: You systematically analyze each operational component to uncover areas where work slows down or resources are wasted. For instance, you might discover that an approval process requiring five different signatures creates unnecessary delays in project completion.
- Enhance resource utilization: Through careful examination of how your organization uses its people, technology, and materials, you can identify opportunities to optimize these resources. This might involve discovering that certain expensive equipment sits idle during specific shifts or that staff expertise isn't being leveraged effectively.
- Ensure alignment with organizational goals: You evaluate whether daily operations and processes actually contribute to achieving your strategic objectives. This assessment helps you identify legacy practices that are no longer useful.
- Improve risk management and internal controls: By examining operational procedures, you can identify potential risks and control weaknesses before they become problems. For example, you might find that certain critical processes rely too heavily on a single employee's knowledge — which creates operational vulnerability.
- Support continuous improvement initiatives: Regular operational audits are a systematic approach to improvement. They help you establish benchmarks and measure progress toward operational excellence over time.
Common types of operational audits
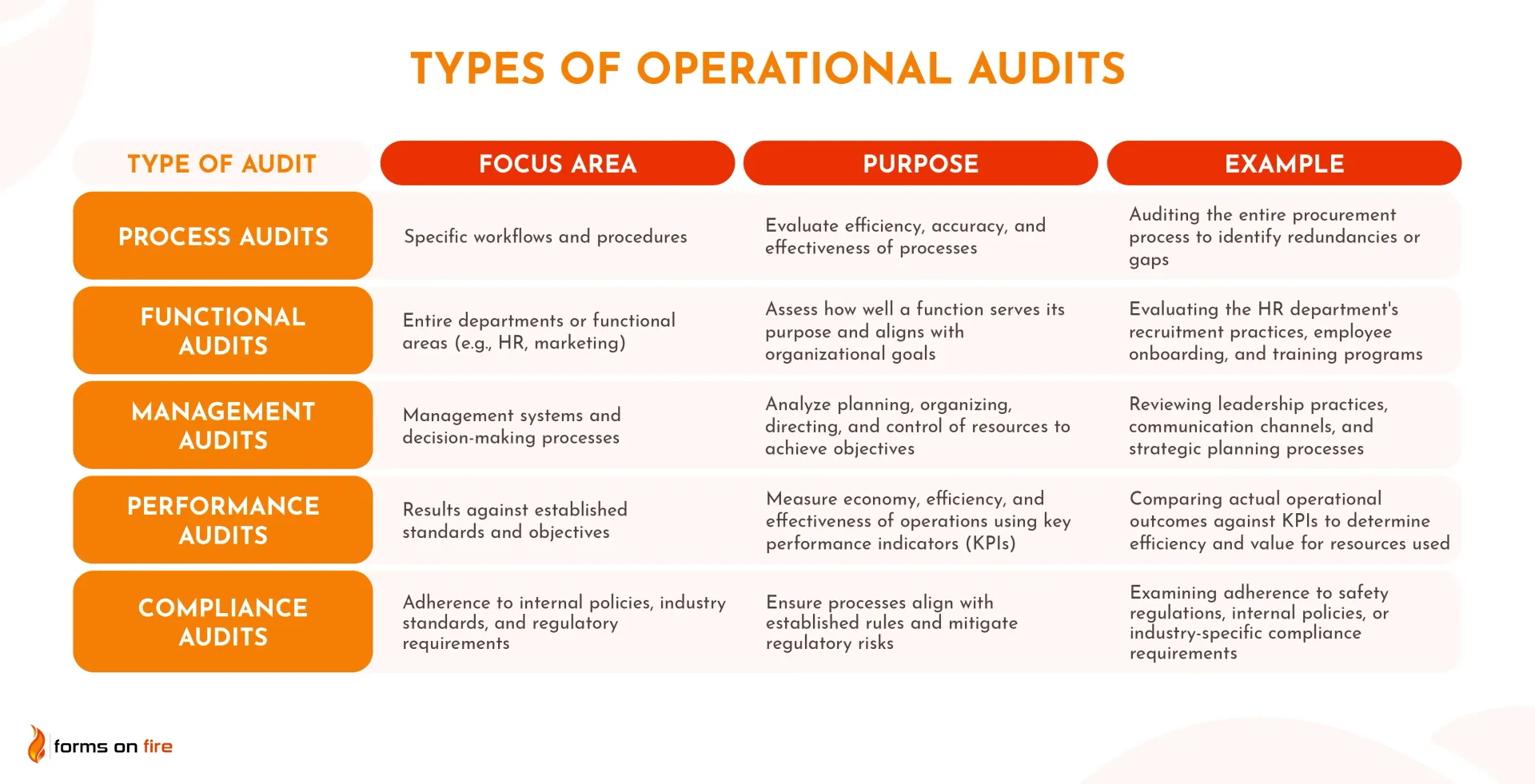
Operational audits come in several forms, each designed to evaluate specific aspects of your organization's operations:
- Process audits: These focus on evaluating specific workflows and procedures within your organization. You'll examine individual steps, documentation, and efficiency of processes to ensure they operate as intended.
- Functional audits: These examine entire departments or functional areas of your organization, such as human resources, marketing, or operations. You'll assess how well the function serves its purpose and supports organizational goals
- Management audits: You'll analyze how well managers plan, organize, direct, and control resources to achieve objectives. This includes reviewing leadership practices, communication channels, and strategic planning processes.
- Performance audits: These measure actual results against established standards and objectives. You'll evaluate the economy, efficiency, and effectiveness of operations using key performance indicators (KPIs).
- Compliance audits: These verify adherence to internal policies, industry standards, and regulatory requirements that govern your operations. You'll examine procedures, documentation, and practices to ensure they align with established rules and regulations.
You need to understand these different types to select the most appropriate approach based on your objectives and the areas you need to examine most closely.
How a typical operational audit process looks like
Conducting an effective operational audit follows five essential phases that build upon each other to create lasting organizational improvement. Let's examine each phase in more detail.
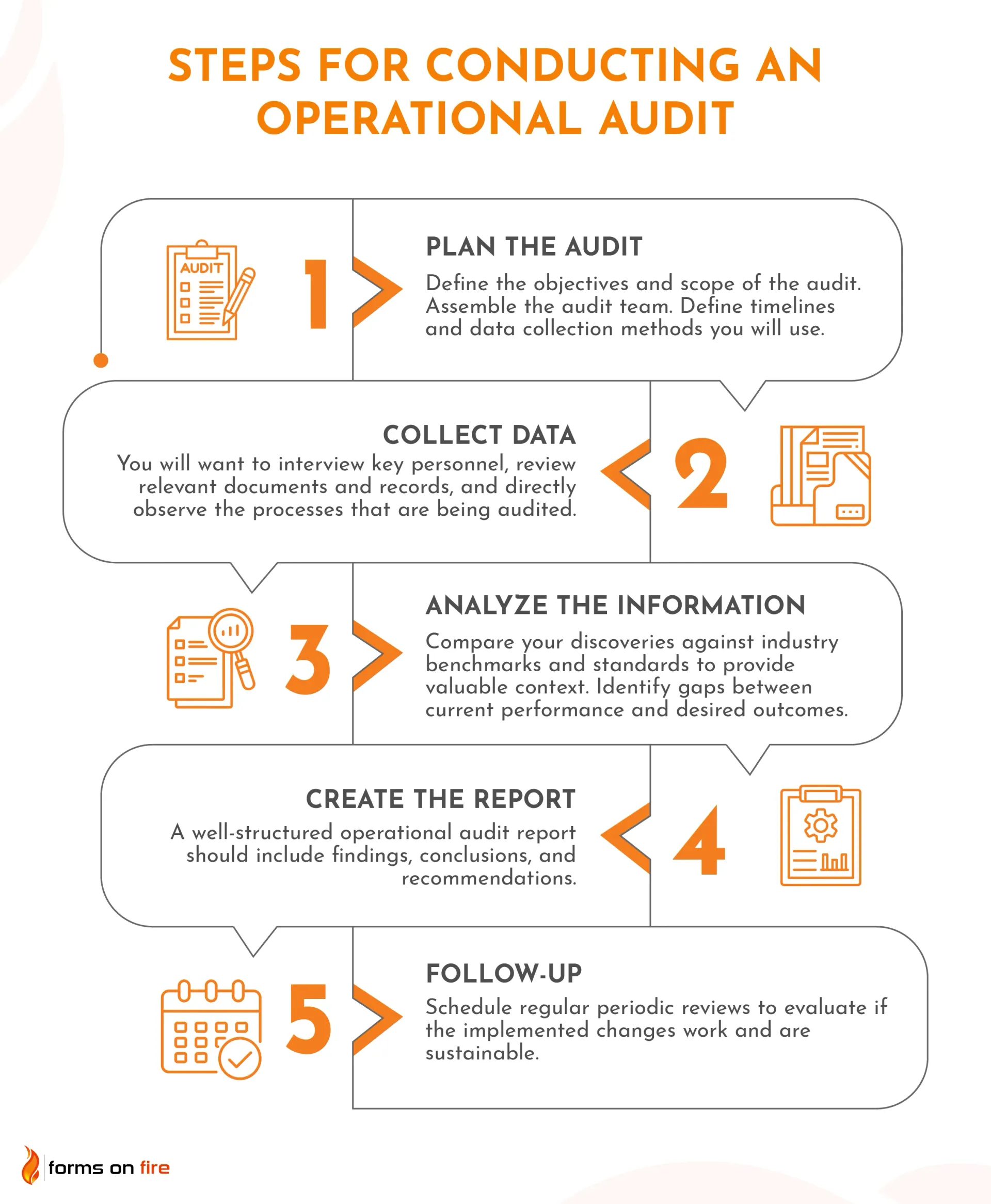
1. Plan the audit
To establish the framework that will guide your entire audit process, you need to define four items:
- Objective and scope of the audit
- Audit team
- Rough timeline
- Data collection methods the audit team will use
Defining objectives and scope requires you to specify which areas, processes, or functions you'll examine in your audit. Rather than broadly stating "improve efficiency", specify that you want to "reduce the order processing time by identifying bottlenecks in the fulfillment process".
The audit team should include a mix of expertise. Consider both technical knowledge of the processes being audited and specialized audit skills. If you're auditing manufacturing processes, you'll need team members who understand lean manufacturing principles alongside those skilled in data analysis and audit methodology.
Your timeline and checklist serve as your operational roadmap. Break down the audit into distinct phases with specific milestones and deadlines, accounting for preliminary research, data collection, analysis, verification, and report preparation. Build in buffer time for unexpected challenges or deeper investigation of issues that emerge during the audit.
Your data collection methods must align with your audit objectives. Combine quantitative methods like statistical sampling and performance metrics with qualitative approaches such as employee interviews and direct observation. This balanced approach ensures you capture both measurable performance data and valuable contextual insights.
2. Do the groundwork and collect data
Groundwork and data collection form the core of your operational audit, where you gather the evidence needed to evaluate processes and identify improvement opportunities. The quality and comprehensiveness of your data collection directly impact the value of your audit findings.
Three primary methods drive effective data collection in operational audits:
- Interviews with key personnel: These conversations provide invaluable insights into how processes actually work versus how they're designed to work. When you interview staff, ask open-ended questions about their daily challenges, workarounds they've developed, and suggestions for improvement.
- Review of documents and records: Examining documentation helps you understand established procedures, track performance metrics, and identify compliance gaps. This includes analyzing process documentation, performance reports, quality control records, and relevant correspondence that shows how work flows through the organization.
- Direct observation of processes: Some workflow inefficiencies, communication barriers, and potential safety issues only become apparent through careful observation by a neutral party. Take detailed notes about what you see, including timestamps and specific locations.
That said, there are other methods you can use as well.
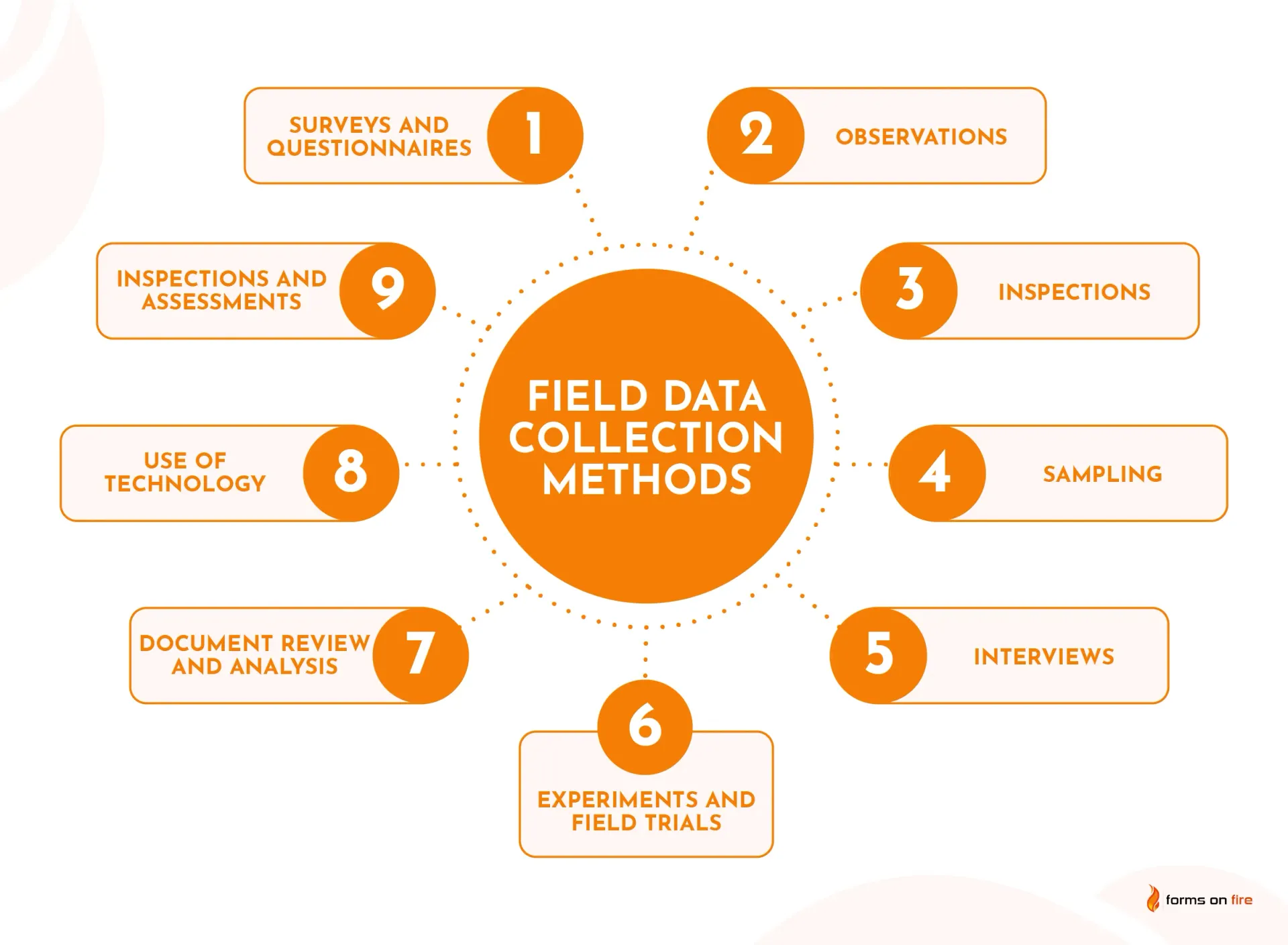
To ensure your data collection is systematic and thorough, use digital tools to document your findings.
For example, you can quickly build custom audit forms and checklists with Forms On Fire that will standardize data collection across your audit team. This will reduce errors, allow you to easily attach photo and video evidence, and simplify the rest of the operational audit process — data analysis and reporting.
3. Analyze the information
In the analysis phase, you'll transform your collected data into meaningful insights that can drive real organizational change. Think of this as assembling a puzzle where each piece of information reveals a clearer picture of your operations' health.
When synthesizing findings, compare your discoveries against industry benchmarks and standards to provide valuable context. For instance, if your order fulfillment takes 48 hours while industry leaders complete it in 24 hours, you've identified a clear opportunity for improvement. This analysis helps you understand not just where you are, but where you could be.
As you examine your data, identify gaps between current performance and desired outcomes, along with potential risks and opportunities. You might discover that what appears to be a staffing issue stems from inefficient scheduling practices, or that communication bottlenecks create unnecessary delays.
To prioritize recommendations, consider both the potential impact of each improvement opportunity and its feasibility. Create a matrix that plots these factors against each other — high-impact, easy-to-implement changes should rise to the top of your priority list.
4. Create an operational audit report
Your report serves as the bridge between your detailed analysis and actual organizational improvement. A well-structured operational audit report should include:
- Findings: Present your discoveries objectively, supported by solid data and evidence. Each finding should detail what you observed during the audit, including specific examples, metrics, and patterns identified.
- Conclusions: Draw clear connections between your findings and their implications for the organization. Explain what these findings mean for operational efficiency, risk exposure, and business objectives.
- Recommendations: Provide specific, actionable steps for improvement based on your findings and conclusions. Ideally, your recommendation should include implementation requirements (e.g. software to automate a workflow) and expected benefits.
You can find some templates online if you want to present findings in a nice-looking document (and don’t have time to build one from scratch).
When you present to stakeholders, tailor your message to different audiences. Senior leadership will focus on strategic implications and resource requirements, while department managers need to understand specific operational changes affecting their areas.
Create opportunities for open dialog rather than simply presenting findings — this will help build buy-in for your recommendations.
5. Follow-up
This phase ensures your recommendations create lasting positive change.
Monitoring the implementation of recommendations requires a systematic approach. You'll need to establish clear metrics and milestones to track progress effectively. For instance, if you recommended streamlining a procurement process, you might monitor the reduction in processing time over several months.
Schedule regular periodic reviews (perhaps twice a year) to evaluate if the implemented changes are sustainable and achieving desired outcomes. During these reviews, gather feedback from affected staff and analyze performance data against your baseline measurements.
This way, you’ll fine-tune improvements and ensure positive changes become permanent.
Common tools and techniques for operational auditing
Successful operational audits rely on a combination of digital tools and proven analytical techniques that work together to enhance your findings. Let's explore them further.
Digital tools
Digital tools have revolutionized operational audits, making the process more efficient and your findings more reliable. Features like photo documentation, automatic timestamping, and real-time collaboration at your fingertips transform how you gather and manage audit evidence.
Another benefit of using digital tools to collect audit data is the ability to instantly generate reports. This simplifies both data analysis and reporting.
Visualizing complex processes becomes a lot clearer with modern flowcharting software. Just as a well-drawn map helps you navigate unfamiliar territory, digital flowcharts help you identify bottlenecks and inefficiencies more easily. These have become a staple in business process optimization.
Helpful techniques
SWOT analysis serves as your systematic framework for evaluating the complete picture of your operations. This analysis can be performed at the level of a department or even a process. It can help you identify areas you need to focus on for operational audits.
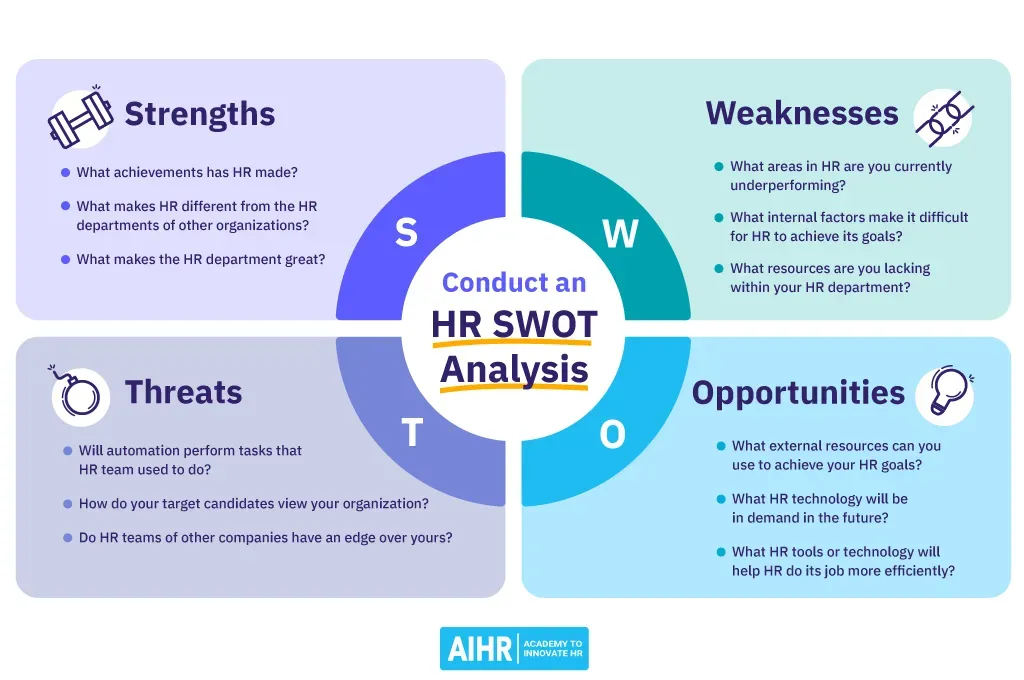
Benchmarking guides you toward operational excellence by showing you what's truly possible in your industry. Study how high-performing organizations achieve their results, then adapt their successful strategies to your own operations while setting targets that challenge yet remain achievable.
Root cause analysis (RCA) transforms you from a problem spotter into a problem solver by revealing the true source of operational challenges. Is it a technical, resource, personal, process, leadership, or client issue? RCA will help you find out the root causes so you can give proper improvement recommendations.
Simplify operational audits with Forms On Fire
Forms On Fire can help you transform your operational audit process by digitalizing every step, from data collection to reporting.
Think of it as your audit command center where you'll create custom forms, manage data collection, and generate powerful insights. You'll spend less time on administrative tasks and more time on what matters — analyzing operations and recommending improvements.
If you conduct internal audits regularly, Forms On Fire can save you an enormous amount of time by standardizing the whole audit process. The mobile forms and checklists you build for one type of audit or process can be quickly adjusted and reused for other types.
On top of that, as a no-code form builder, you can also use the Forms On Fire platform to digitize other processes at your organization.
Need more information? Reach out to our team or schedule a quick product demo.